Material Handling
Conveyor Technology
To optimize, rationalize and automate Jasan Automation Pvt Ltd, has vast experience in material flow software solutions.
Electro Monorail System
An EMS system is an electric monorail system that carries parts individually to each workstation. It is an overhead rail-bound means of conveyance with individually driven carriers, which move independently on the rail system. The track consists of joined section rails and integrated busbars, which can be extended to the desired length. Electrified monorails are one of the fastest goods transport systems that can be set up in a warehouse. Electrified monorails are widely used in warehouses and production centres due to the countless benefits.
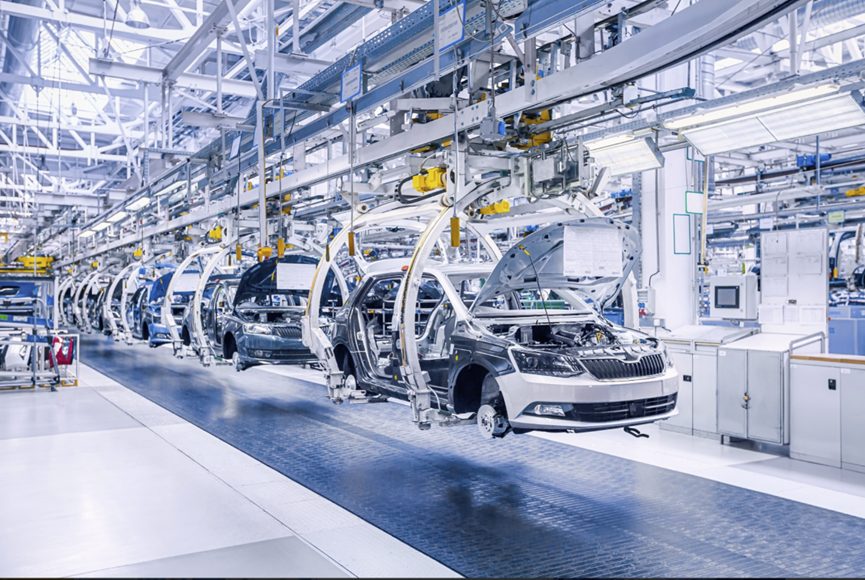
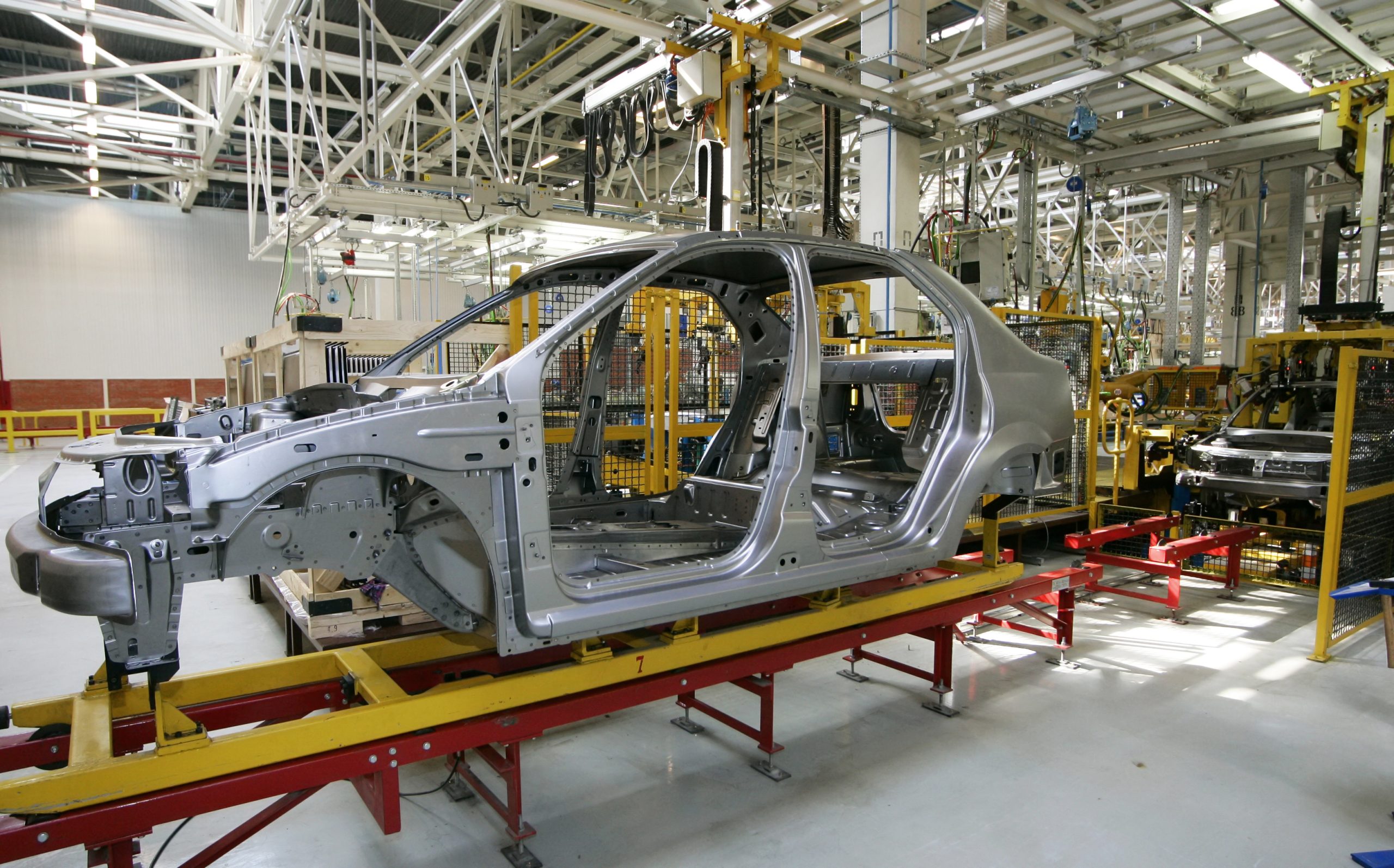
Skid Conveyors
Skid Conveyors generally carry products on fixtures with two longitudinal runners called skids. Skids are conveyed both longitudinally (direction of travel parallel to skid rails) and transversely (direction of travel perpendicular to skid rails). The types of conveyor sections utilized include VDL, Cross Transfer, Powered Roller Lift Tables, Hold Tables, Powered Roller Bed, Turntables, Pivot tables, Shuttle Carriage, Scissors Lift and Skid Stacker/Destacker.
Belt Conveyors
Belt conveyors are the most commonly used bulk handling conveyors in history due to their reliability, versatility, and range of capacities. Materials from small to large can be transported on a belt conveyor. The conveyor belts are are often application-specific and are used in a wide variety of material transport applications such as manufacturing, food processing, automobile and heavy bulk handling.
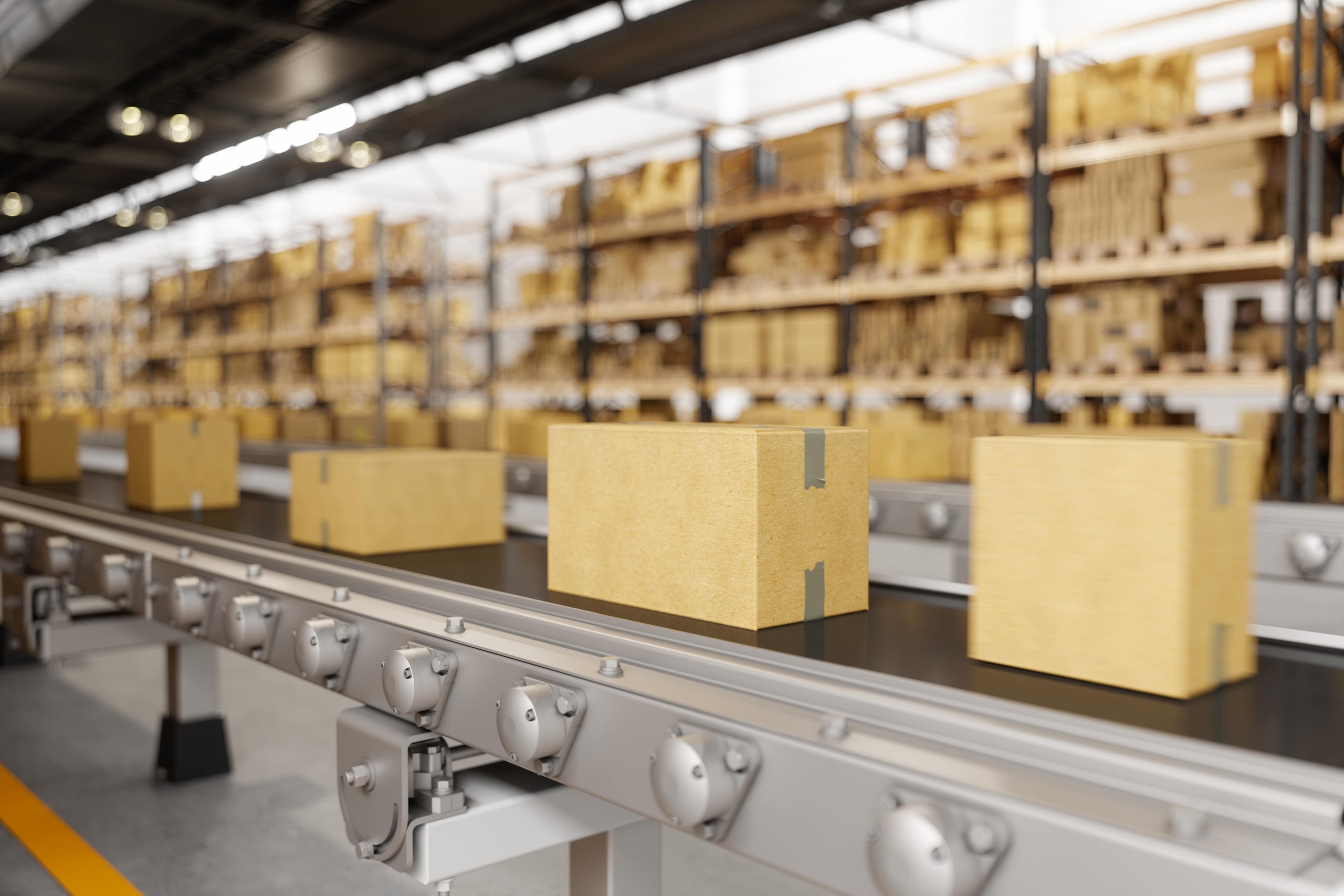
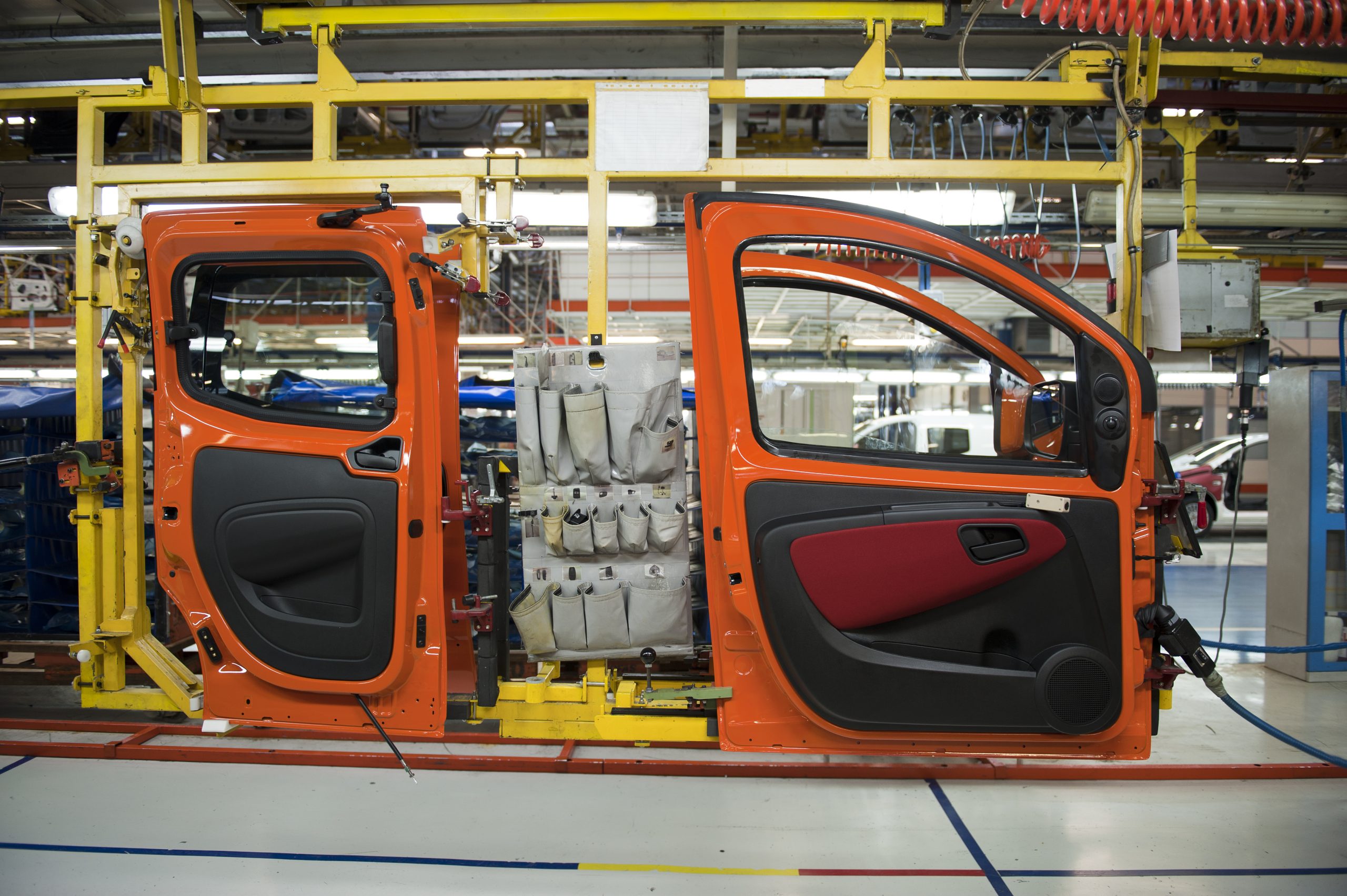
Overhead/Inverted Power & Free Conveyor
Overhead Power & Free Conveyors have free trolleys that are driven by power chains and carriers that transport the material to a given location. The carriers are attached to the free trolleys and are normally engaged to the power chain by an attached pusher dog assembly on the free trolley. The pusher dog can be disengaged by a cam action in either the free trolley or the chain dog, caused by accumulating behind another free trolley or by engaging a stop blade. The chain continues to move while the carrier becomes temporarily stationary until the free trolley becomes re-engaged with the chain. An Inverted Power and Free Conveyor utilizes a single enclosed track combining the power chain and the free trolleys. The power & free system uses fixed chain dogs that engage the pivotal free trolleys to move them through the system. Disengaging the free trolley from the chain dog allows for free trolley accumulation. Areas of use include production areas or delivery systems that require accumulation such as general assembly, body shop, painting and oven drying.
Roller conveyors
Roller conveyors feature steel rollers along a conveyor line. The rollers are in direct contact with the items being conveyed – boxes, cartons, totes or pallets, for example. These durable conveyor systems are often leveraged to convey heavier, non-fragile items that have stable and solid bottoms for secure handling
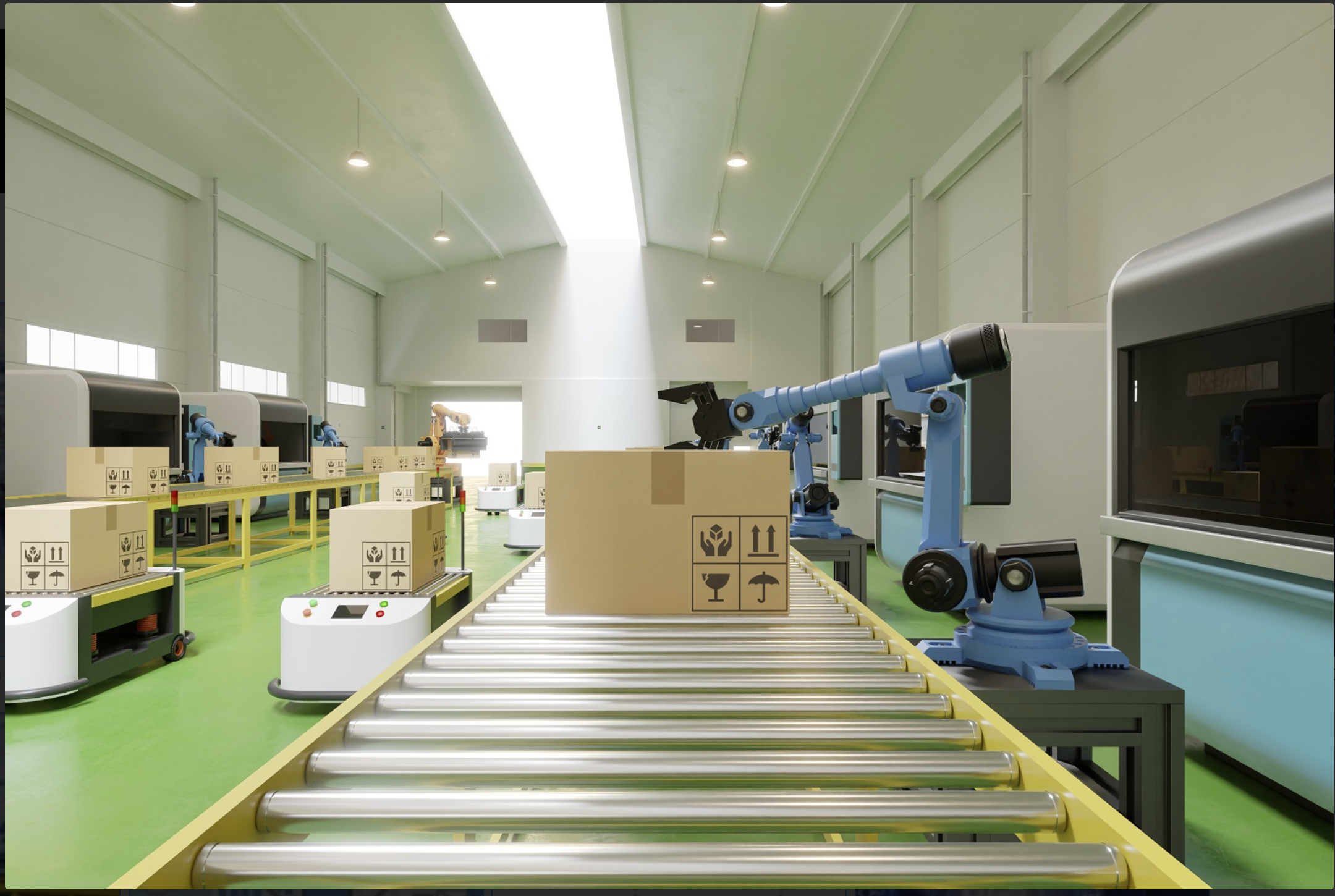
Automated Storage & Retrieval Systems (ASRS)
Modular, flexible and software-driven ASRS for maximum efficiency An Automated Storage and Retrieval System is to store goods in defined locations and retrieve them when necessary. ASRS have gained popularity and offer solutions that fit any business, thanks to their flexibility, size variety, and budget diversity.
Where to Use Automated Storage and Retrieval Systems
ASRS are typically used in manufacturing, warehouses, and distribution areas to help organize a high volume of items that need to be stored and moved, and to optimize space. From the automotive and manufacturing industries to retail and pharmaceuticals, ASRS redefine workflow and the use of physical, financial and human resources. An automated storage and retrieval system reduces labor cost, optimizes inventory control and boosts shipping speed
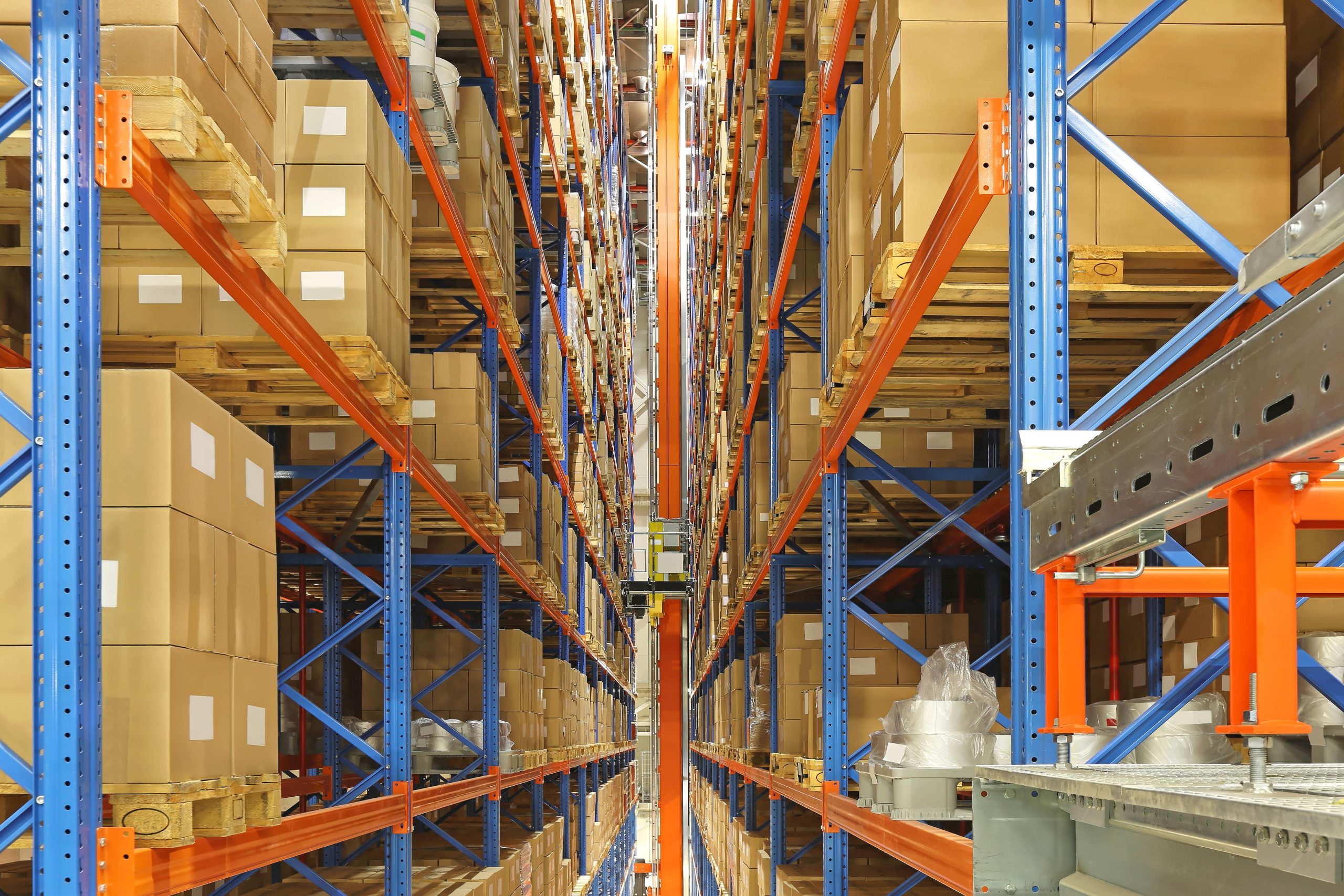
Automated Guided Vehicles (AGV)
AGV
Automated Guided Vehicles (AGVs) transport and store a wide range of products and materials in a variety of industries and operations — factories, warehouses, distribution centers, and shipping areas. AGVs are a safe and secure way to increase process efficiency and improve business profitability. AGV systems operate autonomously, eliminating human errors that can cause costly damages and mistakes when picking and loading. Individual AGVs are exchangeable, which ensures redundancy in system operation.AGVs provide a safe and secure way to increase process efficiency and improve business profitability — all without human intervention. AGVs can automatically lift, rotate, and shift loads. They can carry loads to and from racking, and store and retrieve them in block-stack or deep-stack lanes over 10 meters high. They can transport loads over long distances to deliver them to and collect them from a wide range of conveyors and processing machines.
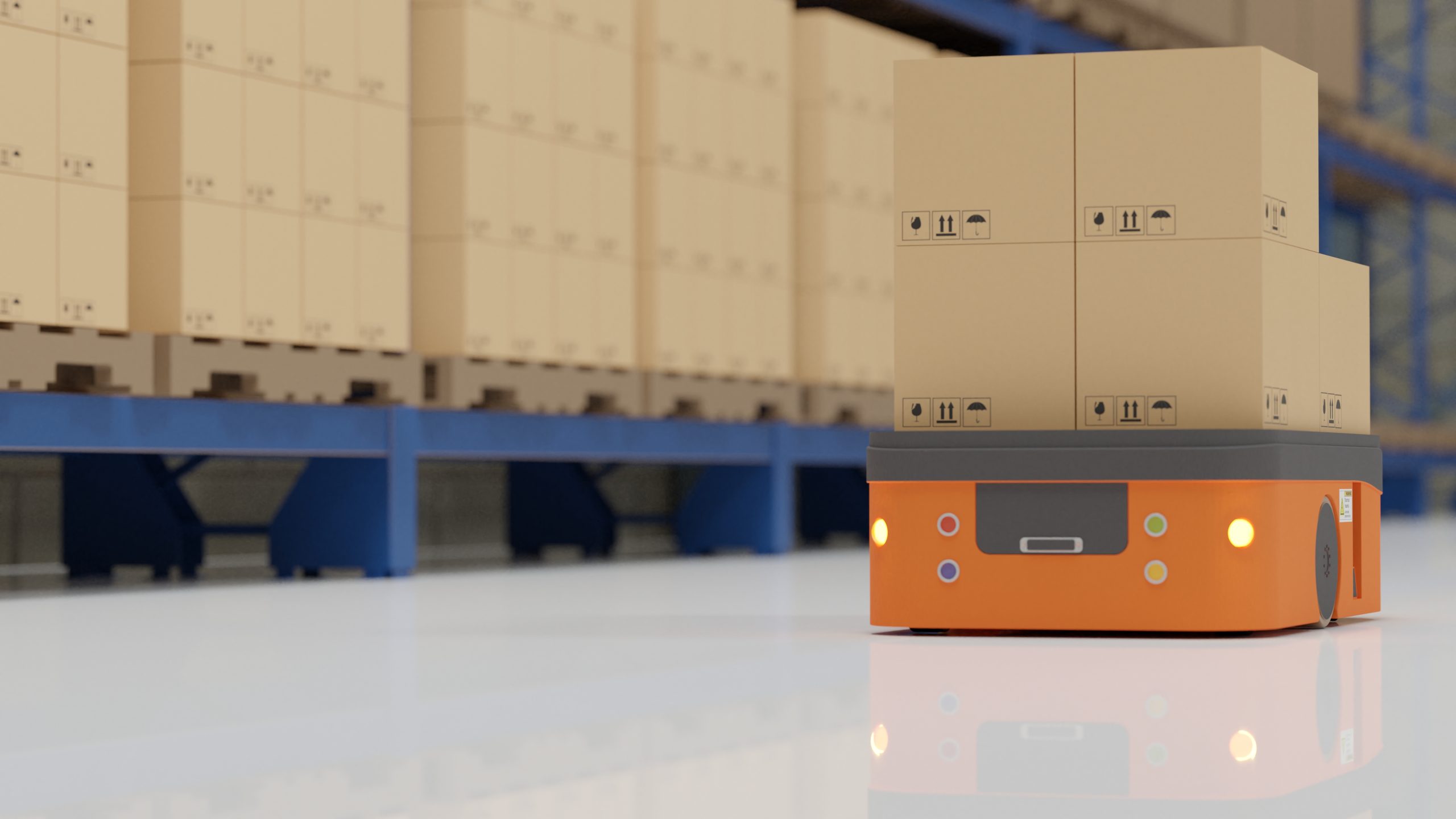